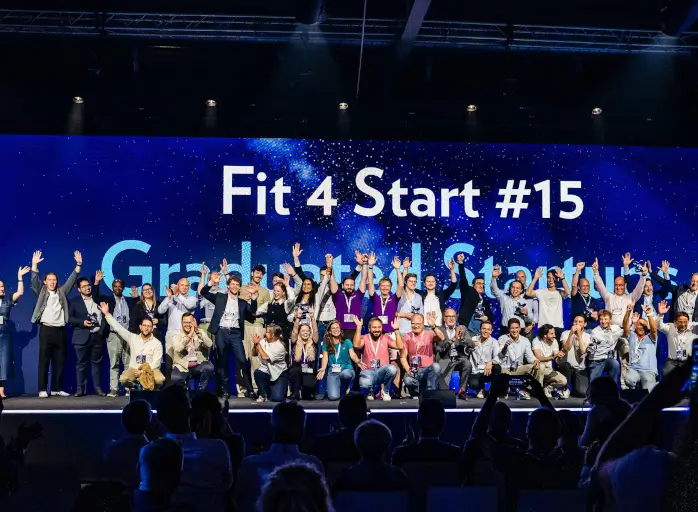
At the beginning of June, as part of the 2023 edition of Smart Manufacturing Week, a special day dedicated to the construction sector provided an opportunity to review a number of key issues that are central to the day-to-day concerns of professionals.
Concrete action and exchanges. This was the theme of the “Construction Day” that was part of the Smart Manufacturing Week organised by Luxinnovation at the beginning of June.
The morning was devoted to a visit to the site of the modular pavilion built by Degotte for the École du Brill in Dudelange. This transitional structure, which is being built in parallel with the renovation of the old school building, must meet the standards required to accommodate children in primary school for the next 6 to 8 years.
From many points of view, such “modular” sites offer advantages over “traditional” ones. “A modular building can always be dismantled and have a 2nd, 3rd or even 4th life before being dismantled for good and having its raw materials recycled,” explained Benoit Keyen, Development Director at Degotte.
The morning continued with a virtual visit to the workshops of Hyperion Robotics, a start-up based in Heslinki (Finland) and specialising in 3D concrete printing. Its ambition is to revolutionise the world of concrete, both technologically and ecologically, bearing in mind that 8 -10% of global greenhouse gas emissions come from concrete production alone – twice as much as from air transport.
“One of the answers to this problem is 3D printing,” said Henry Unterreiner, one of the company’s founders. “This guarantees mechanical performance similar to that of traditional concrete, but using 75% less material.”
The figures of the process speak for themselves: a 90% reduction in the carbon associated with concrete construction, a 30% saving in terms of costs and a 50% reduction in production time. “Not to mention the gains in terms of safety.”
A live performance demonstrated the speed of the process, with the start of erection of a 1.72 m high retaining wall made from a total of 86 layers of concrete.
The afternoon of this special day was dedicated to two round tables organised at the Neobuild premises, the first of which was devoted to the theme “Decarbonisation via ‘off-site’ construction: reality or fiction?”.
“The impetus for all the thinking around decarbonisation must come from the client. By incorporating these parameters from the outset, we can achieve savings of several hundred euros per square metre,” explained Raphaël Leduc, Project Director at property developer Codic.
Obviously, the issues and expectations are not the same for “industrialisation” versus the “pre-fabrication” approach. “We shouldn’t pit prefabrication against industrialisation, but rather take the best of both,” said Omar Mataar, Innovation Director at CLE / Wood Shapers.
Prefabrication and modularity are two promising responses to the current challenges of sustainability and the circular economy in the construction sector.
Charles-Albert Florentin (Luxinnovation)
Saving time is obviously one of the main levers for implementing such approaches. “It’s always better to assemble in five hours than to build in five days,” explained Benedito Lemos, International Coordinator at Casais, one of Portugal’s leading construction companies.
The moderator, Luxembourg Cleantech Cluster Manager Charles Albert Florentin at Luxinnovation, concurred with the presentations made at the round table. “Prefabrication and modularity are two promising responses to the current challenges of sustainability and the circular economy in the construction sector. They contribute not only to optimising the sector’s carbon footprint, but also to the development of activities such as renovation, deconstruction and re-use.”
Construction company CDCL highlighted the partnership established with CREE, a company based in Austria that has revolutionised the world of construction by proposing a modular wood-concrete system: traditional materials, but implemented using innovative techniques. The result is shorter construction times, much lower CO2 consumption and improved energy performance. “Off-site construction and industrialisation make it possible to consolidate lots that are often split up into smaller units, and to generate enormous savings in terms of transport, with almost 30% less tonnage,” explained Quentin De Man, Head of Design for Build at CDLC / CREE.
Installing and hanging a prefabricated concrete stairwell can be done in a matter of minutes, compared with three months for an on-site project. In this case, the time saved speaks for itself. “Producing such a structure upstream, in our factory, also means that we are free from constraints due to bad weather. It also ensures greater safety for our workers,” said Roméo Martins, Lean Methods Stability Manager in the Greenstone design office.
Prefabrication is also in the genes of Prefalux, a general contractor specialising in timber construction, roofing and finishing. The benefits of this approach can also be measured in terms of energy efficiency. “By maximising prefabrication on our sites, we can limit the nuisance caused by transport,” explained Pierre Goetschy, Technical Director at Prefalux. “We also recover 80% of our energy thanks to the photovoltaic panels installed in our workshops, and all our wood chips and waste are taken to Luxenergie, another source of energy for us.”
The topic of the second panel took a more in-depth look at a specific issue, raising the question of the role of technology in the prefabrication of components and modules.
Ferd Feidt, managing director of Bétons Feidt, argued: “We can achieve great things if we don’t take away the right to be creative. The robotisation of certain repetitive processes, such as setting up formwork or cutting materials, are not technological revolutions as such. It’s more a question of our responsibility to improve certain processes.”
Industrialisation and technology can be found at many levels in the vast range of construction trades. Based in the North of France, Les Companions is committed to creating a genuine collaboration between man and machine and, in so doing, providing innovative solutions for all building trades. This is the logic behind Paco, a collaborative robot for painters.
“The painter carries out a complete and precise measurement by performing a 3D scan of the environment, which enables the part to be recreated virtually,” explained Antoine Rennuit, the company’s founder. “The robot is then programmed to define the paintwork to be carried out. The robot will then be in charge of difficult, dangerous or repetitive tasks.”
Robotisation and technology in general will never replace the know-how of professionals.
Mickaël Pascual (Neobuild)
However, there is no question of the machine replacing the human. The intervention of the professional painter is still required. “The technologies are there to support and provide certain solutions to the problems encountered on a daily basis, both by those who build the buildings and those who will use them.”
Guillaume Weiss, Director of Manufacturing Systems Division at Leko Labs, is no different: “Robots will never replace anyone. They are excellent for repetitive and demanding tasks. In the meantime, we can re-employ staff in a different way.”
The link between man and machine remains, of course, one of the major issues in any move towards automation and robotisation. On this point, all the speakers were unanimous: there is no question of pitting one against the other. “Robotisation and technology in general will never replace the know-how of professionals. They are merely tools that make it possible to respond primarily to the constraints of speed and arduousness of work,” concluded Mickaël Pascual, Project Manager at Neobuild, who moderated this second panel.
A more detailed account of this “Construction Day” will be published in the September issue of Neomag magazine.